exoskeleton

Exoskeleton prototype being built
Mechanical Engineering Masters research project at Imperial College London.
Designed and manufactured a parametric assistive hand exoskeleton for stroke patients in collaboration with the Imperial College / Charing Cross Hospital Stroke Unit and Musculoskeletal Lab.
Of the 150,000 stroke victims a year in the UK, 2/3 survive. More than half of these survivors are dependent on others for everyday tasks. Only 12% of stroke patients recover upper limb function - an essential element of a high quality of life. However, the brain is capable of large scale structural and functional reorganisation following stroke (neuroplasticity).
I wanted to create a completely new design that takes into account the social considerations of clinical design, as opposed to a purely technical engineering project; I feel that it is important for such projects to have the aim of being deployed in industry, and as such importance was put on factors such as social utility and quality of life, cost, ease of use, and aesthetics.
Following substantial literature and field research, the solution presented here is a cost-effective tool that permits rehabilitation through contextually-relevant tasks and objects, independent of healthcare professionals. Contextually-aware tasks promote better compliance and ultimately have been shown to lead to regaining or developing motor function.
Prototype cost was 15% of previous iteration with comparable functionality. The aim was to determine the core functionality of such a device, and streamline the manufacturing so as to make it immediately cost-effective to the National Health Service (NHS).
Final actuated prototype

Jenny, occupational therapist at Charing Cross stroke unit, highlights the lack of appropriate tools in the clinical setting.
Biscuit tins and baked beans cans are the clinical state-of-the-art - all meaningful rehabilitation thus requires substantial time with already oversubscribed health professionals.

Kinematic model for cylindrical grasping
After programming a simplified hand trajectory model on MATLAB, based on previous work done by Thomas Burton, it was found that the number of degrees of freedom can be reduced without significantly affecting hand function and allowing for natural hand trajectories. The number of actuators were reduced from 6 in the previous iteration to just 2, making the pulley system much lighter and usable.

Illustration of pulley system
The kinematic model found that all the distal finger joints were heavily coupled, that is to say had an approximately constant angle ratio between each other. As a result, they could all be mechanically coupled to each other, while only needing one actuator located somewhere proximally on the arm.
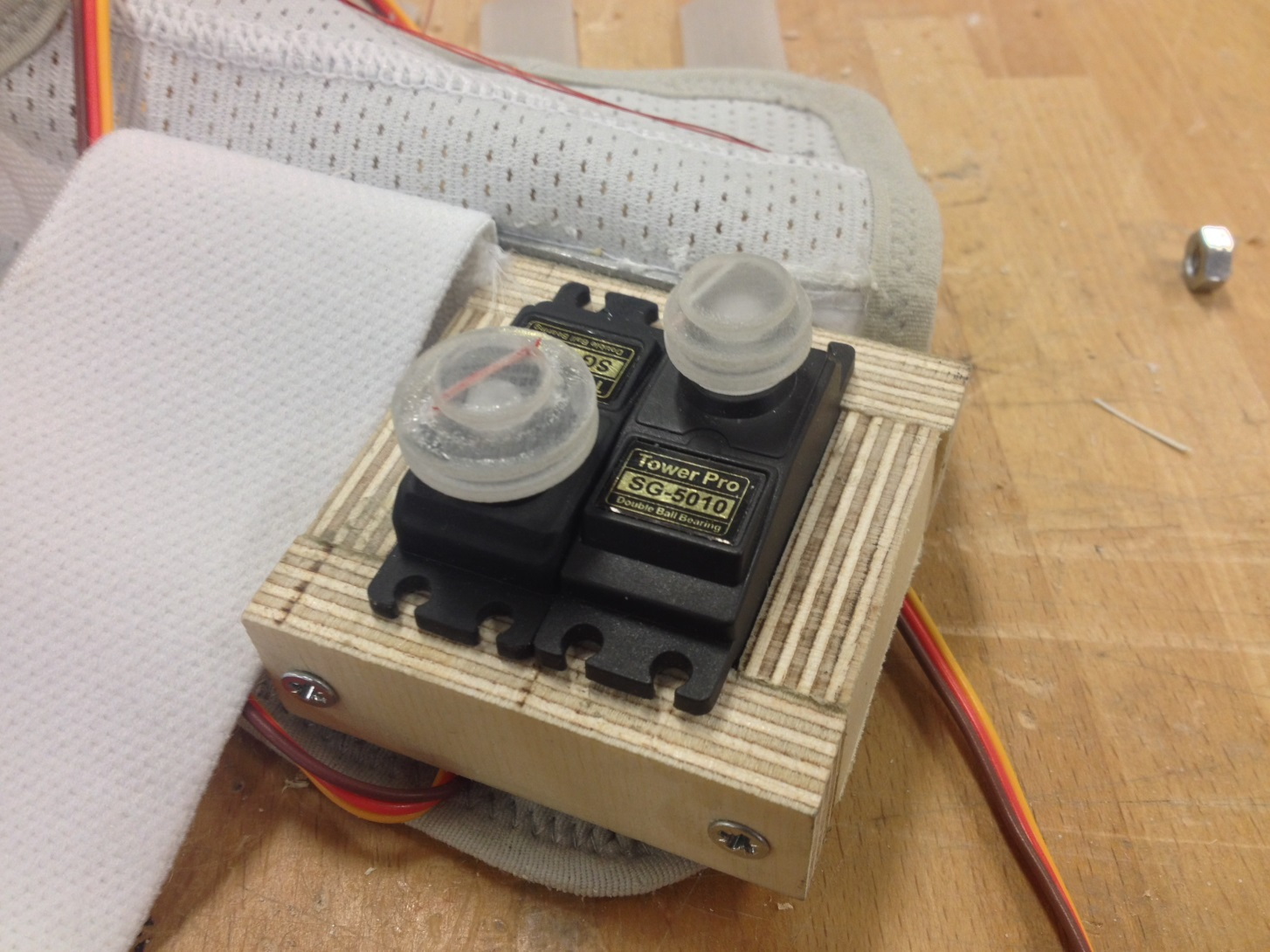
Prototype servomotors and enclosure
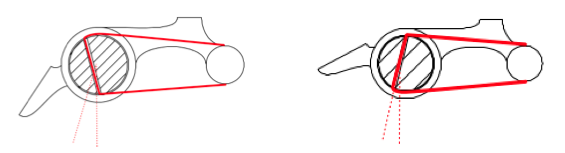
Built-in mechanical safety feature prevents over-flexion (left) or over-extension (right) by the actuators
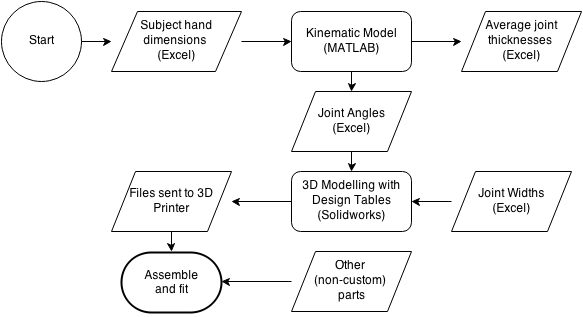
Flow chart of the total manufacturing process, allowing for custom parts to be cheaply manufactured on-site with minimal involvement from health professionals.
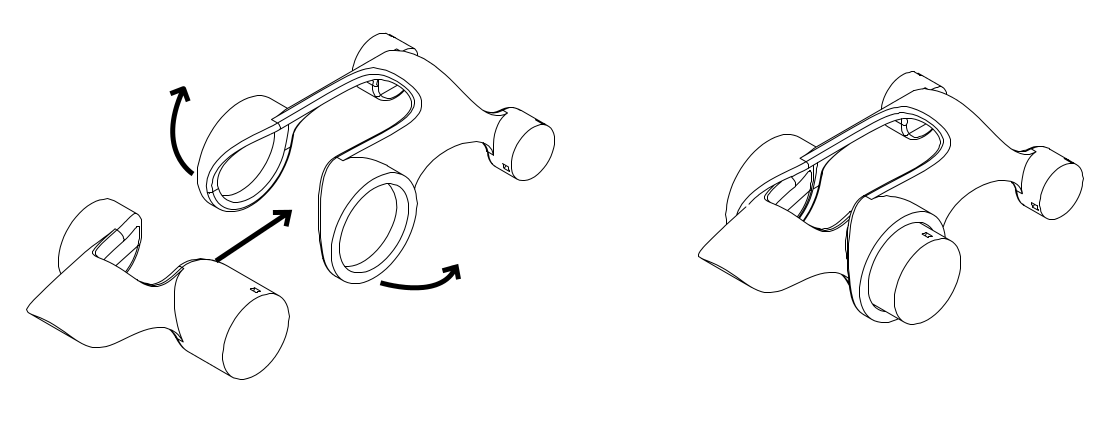
The parts have been designed to streamline the manufacture as much as possible. For example, each of the exoskeletons phalange 'snap-fit' together and have built-in bearings, thus removing the need for fasteners, bearings and the time and expertise required to fit them.

Example of how the parametric design works. The kinematic hand model on MATLAB stores all of the relevant angle data on Excel, which is then interfaced with Solidworks to automatically resize all of the parts to suit the user.